- Regular maintenance checks extend equipment’s lifespan, reduce costs, and minimize downtime.
- Strategic allocation of equipment and resources prevents operational bottlenecks and saves time and expenses.
- Accurate inventory management, like software usage, labeling, regular audits, and avoiding overstocking, maximizes equipment usage.
- Collecting and analyzing data aids in evaluating equipment utilization and boosting operational efficiency.
- Understanding when to replace or upgrade equipment can reduce operating expenses and improve productivity.
As a business professional, you know that managing your warehouse equipment is crucial to keeping your operations running smoothly. However, few realize that properly maintaining and managing this equipment can significantly impact their bottom line. Competition in advanced countries, from Japan and Singapore to Western Europe and the United States, has forced businesses to become more knowledgeable and informed about their warehouse equipment needs. In fact, according
You can save money and streamline your entire operation by keeping equipment in good working order, effectively allocating resources, and efficiently managing inventory. This article will provide tips on managing your equipment to reduce costs and increase efficiency effectively.
Regular Maintenance Checks
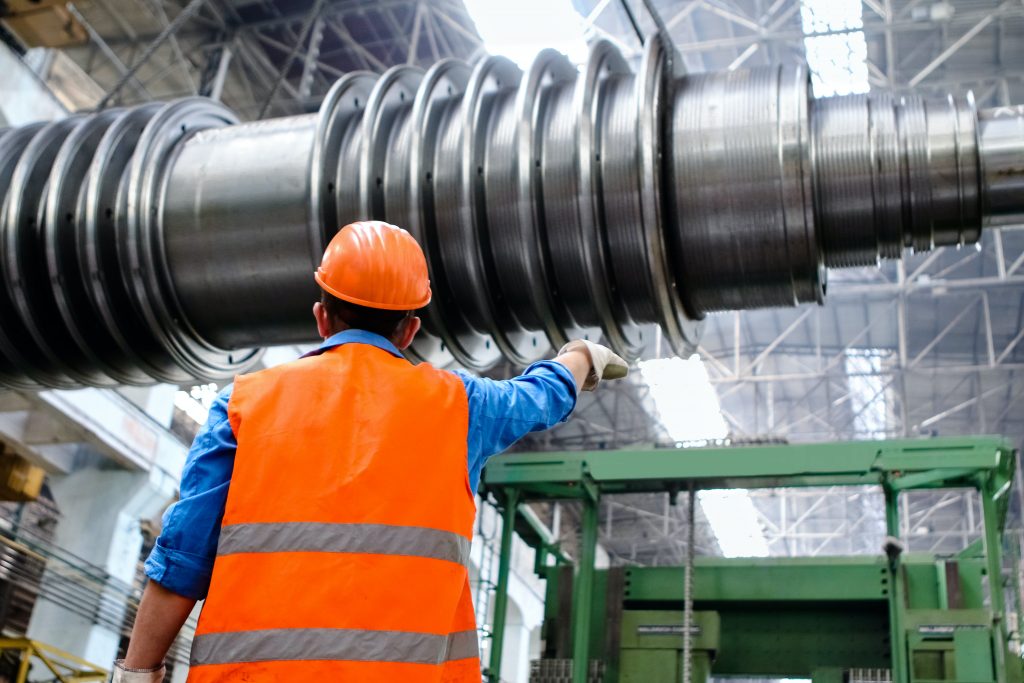
Investing in regular maintenance checks can save your company from major losses due to equipment breakdowns and costly repairs. Simple preventive maintenance activities can go a long way toward extending equipment life, reducing downtime, and minimizing costs. Work with a trusted repair company or hire an on-site mechanic to keep all equipment in good working condition, including regular oil changes, tire rotations, and component inspections. As a result, your equipment will last longer, perform better, and have fewer breakdowns.
Strategically Allocate Equipment and Resources
Properly allocating equipment and resources can save time and expenses, cut down on wait times, and prevent operation bottlenecks. Always consider the size and type of equipment needed for each job as well as the skill level of your staff. Additionally, train your workers to use equipment properly to be used efficiently, minimizing equipment breakdowns and downtime.
Some companies also prefer renting equipment instead of purchasing to save money and avoid equipment depreciation. For example, forklift rental companies offer the latest models, maintenance, and repairs for a fraction of the cost of purchasing new equipment. This flexibility allows businesses to match their equipment needs with the workload, reducing unnecessary costs.
Inventory Management
Maintaining accurate inventory records can help you keep track of all your equipment, ensuring that you are fully utilizing each piece and reducing the need to rent or purchase additional equipment. There are many ways to manage and organize your inventory, so here are a few tips:
Use inventory management software.
To track all equipment and their usage, maintenance schedules, and depreciation, consider using inventory management software. With this tool, you can easily generate reports to analyze equipment usage, identify any issues, and make informed decisions about purchasing or renting new equipment.
Implement a labeling system.
Properly labeling all equipment and keeping an updated record of their location can save time and reduce confusion when searching for specific items. This practice also helps prevent misplaced or lost equipment.
Regularly audit your inventory.
Regularly auditing your inventory is essential to ensure that all equipment is accounted for and in good working condition. It also allows you to identify any discrepancies, such as missing or damaged equipment, and take necessary actions. If possible, assign a dedicated team member to conduct regular inventory audits.
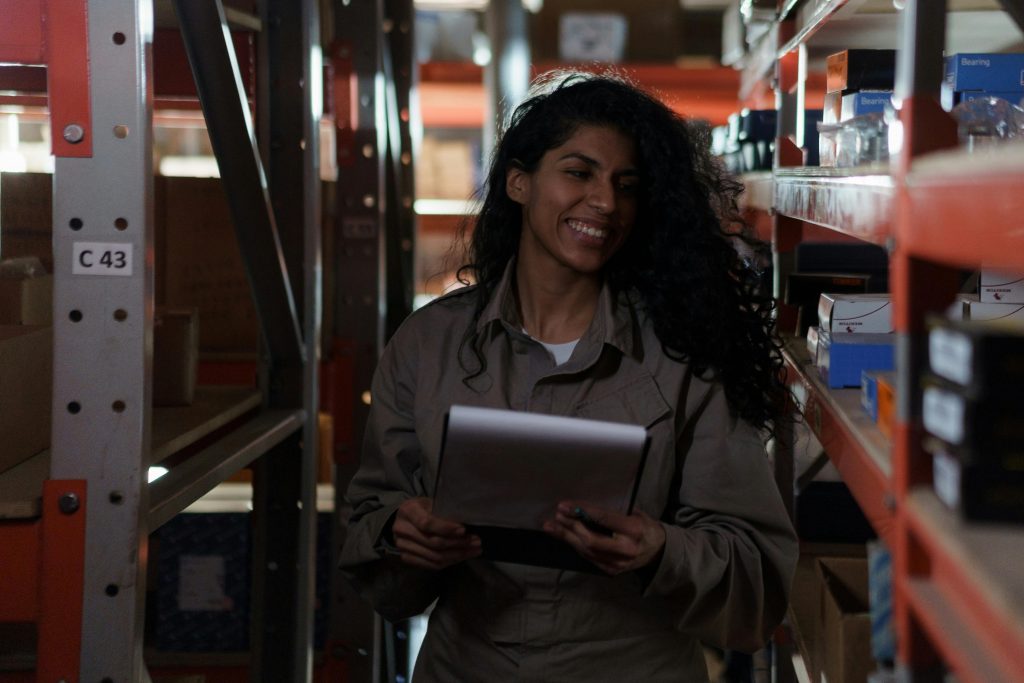
Avoid overstocking.
Overstocking can lead to unnecessary equipment costs and occupy valuable warehouse space. By tracking inventory levels and usage, you can avoid ordering or renting more equipment than you need. You can also plan ahead and schedule maintenance or repairs for equipment during periods of low usage, minimizing disruption to your operations.
Data Collection and Analysis
Collecting and analyzing data can help you evaluate your equipment utilization and identify areas where you can improve operational efficiency. By analyzing data on equipment usage and maintenance activity, you can determine when equipment is underutilized or overused, understand where operation bottlenecks are forming, and optimize routes and scheduling to increase performance efficiency.
Equipment Upgrades and Replacement
Replacing equipment is an inevitable part of warehousing operations. Understanding when to replace equipment is critical to avoiding costly repairs and maintenance. Consider factors like age, utilization, repair frequency, and cost-benefit analysis when debating whether to replace or repair. Upgrading equipment, like optimizing systems, can also reduce costs by improving productivity and reducing operating expenses. If you need help determining when to upgrade or replace equipment, consult experts who can provide valuable insights and recommendations.
Managing your warehouse equipment is crucial to the success of your operation. Following these tips can help you save money and streamline your business processes. Proper regular maintenance, inventory management, and data analysis are key to identifying areas for improvement and making informed decisions about equipment upgrades or replacements. With effective management practices, you can optimize your warehouse operations and stay ahead of the competition.